The Acrylic Vessel (AV)
Cast acrylic was chosen for the AV since it was mechanically strong enough to support the weight of the detector components. The acrylic production was contracted to Reynolds Polymer Technologies (RPT) which was chosen for its ability to limit exposure to radon-laden air (which is a troublesome background for the experiment). The AV was built in three pieces (a truncated sphere, collar and neck) so as to fit in the mine shaft leading underground.
The three acrylic pieces went through different construction processes:
1) the truncated sphere was built from 5 spherical slices, and a spherical cap, that were heated, molded and then bonded together by RPT. The construction of this piece is shown in figures 1a, 1b and 1c.

Fig. 1a: Machining of the spherical slices.

Fig. 1b: Bonding the spherical slices together
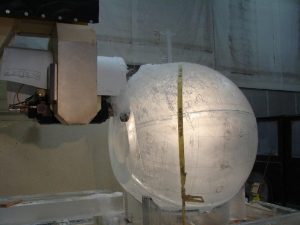
Fig. 1c: Machining of the bonded acrylic sphere.
2) the collar was made from a single sheet of acrylic that was heated and molded to the correct shape (see fig. 1d)
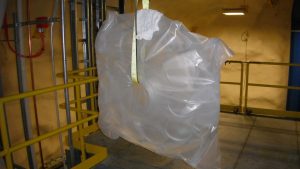
Fig. 1d: Molded neck collar.
3) the neck was made from acrylic sheets that were bonded together to form a cube shape before machining to the desired geometry shown in figures 1e and 1f.
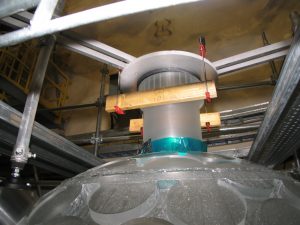
Fig.1e: Neck bonded to acrylic vessel.
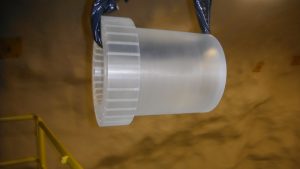
Fig.1f: Machined acrylic neck.
The AV was machined to it’s final spherical shape at the University of Alberta. Spherical stubs were also machined onto the acrylic vessel to allow acrylic LGs to be bonded to the AV. The three pieces were then shipped to SNOLAB and transported underground where RPT completed the bonding of the AV.

Fig.2a: AV machined to final shape.
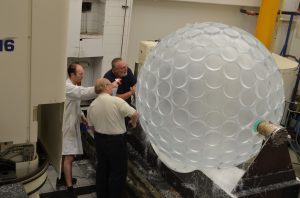
Fig.2b: AV post machining of spherical stubs.

Fig. 2c: AV completely bonded and suspended underground at SNOLab.
The Light Guides
Acrylic LGs, shown in 3a, are used to couple the AV to PMTs allowing optical photons emitted from the liquid argon to be transported to the photodetectors. The thermal properties of acrylic allow the liquid argon inside the AV to be held at cryogenic temperatures while the PMTs at the opposite end of the LG can be operated at roughly room temperature. The length of the LGs was chosen to prevent backgrounds originating in the PMT glass from reaching the liquid argon, and the specific type of acrylic used for LG construction was chosen to limit transmission of UV light that could be generated from backgrounds.
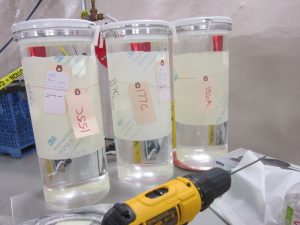
Fig.3a: Cylindrical light guides prior to bonding.
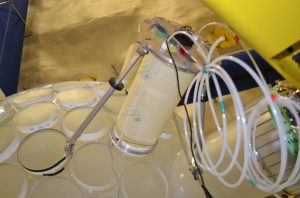
Fig.3b: Bonding of the lighguides to the AV with the designed tripod system.
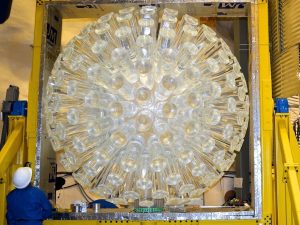
Fig.3c: Completed bonding of the light guides to the AV.

Fig.3d: Reflective material wrapped around the bonded light guides
The 255 LGs, each 0.45 m long and 0.19 m in diameter, were constructed at TRIUMF in British Columbia, Canada. The LGs were then shipped underground to be attached to the AV. A tripod system was developed to bond the LGs to the acrylic stubs machined on the AV, partially shown in fig. 3b. A photo of the AV and LG’s post bonding is shown in fig. 3c.
Roughly 80 percent of the light emitted by liquid argon is trapped inside the LGs by total internal reflection. An additional reflective material was also wrapped around each light guide to increase light collection as shown in fig. 3d.
After that, the next step in the detector construction was optically coupling the PMTs to the end of the LGs.